Warto wiedzieć
Warto wiedzieć
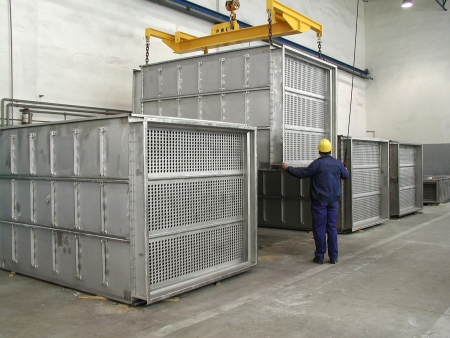
Technologia
Trawienie stali o podwyższonej zawartości chromu i niklu, stosowane jest w celu uzyskania czystej, dobrze zabezpieczonej przed korozją powierzchni detalu. W trakcie procesu trawienia następuje usunięcie wierzchniej warstwy materiału, przebarwień po spawaniu, pozostałości ścierniwa, zgorzeliny, olejów i smarów. W wyniku reakcji chemicznych wydziela się wodór, który przyspiesza złuszczanie się oraz odpryskiwanie tlenków powstałych podczas spawania. Czas trawienia zależy głównie od składu chemicznego stali oraz temperatury procesu. Temperatura kąpieli może przyspieszyć proces trawienia (wyższa temperatura) lub go wydłużyć (niska temperatura). Wizualnym efektem trawienia chemicznego jest uzyskanie matowo-szarej powierzchni detalu. Trawienie może być końcowym etapem obróbki chemicznej detalu lub jedynie procesem wstępnym przed procesem polerowania elektrochemicznego. Wyroby można skierować do procesu trawienia, gdy w składzie stali minimalna zawartość chromu stanowi 18 %, a niklu 8%.
Na skalę przemysłową trawienie prowadzi się najczęściej przy użyciu mieszaniny dwóch kwasów – kwasu fluorowodorowego oraz kwasu azotowego o mocnych właściwościach utleniających. Dodatkowo w celu optymalizacji przebiegu procesu, do mieszaniny trawiącej dodaje się inhibitory organiczne. Sam proces może być realizowany na 3 możliwe sposoby:
- trawienie zanurzeniowe – detal umieszczany jest w wannie galwanicznej wypełnionej mieszaniną kwasów,
- trawienie natryskowe – mieszanina trawiąca jest natryskiwana na cały detal przy użyciu urządzenia ciśnieniowego – w tym przypadku wielkość detalu nie jest ograniczona wielkością wanny galwanicznej,
- żelowanie – smarowanie pędzlem spawów detalu przy użyciu gęstej pasty trawiącej (żelu).
Po zakończeniu procesu trawienia obrabiane przedmioty należy dokładnie wypłukać. Wodę użytą do płukania detali po trawieniu należy zneutralizować odpowiednim roztworem zasadowym, a powstały osad przekazać wyspecjalizowanej firmie zajmującej się utylizacją odpadów.
II. Pasywacja stali nierdzewnych i kwasoodpornych
Pasywacja jest to proces przechodzenia metalu w stan pasywny, w którym podwyższa się jego potencja standardowy. Efekt ten jest osiągany dzięki wytwarzaniu na powierzchni metalu warstwy tlenkowej. W przypadku stali szlachetnych warstwa ta składa się głównie z tlenków chromu. Pasywacja stali nierdzewnych i kwasoodpornych może mieć dwojaki charakter. Może być samoczynna – zachodząca w środowisku zawierającym tlen (czyli w powietrzu lub dobrze natlenionej wodzie) lub wymuszona – zachodząca pod wpływem silnie utleniającego kwasu jakim jest kwas azotowy V. O ile warstwa pasywna wytworzona samoczynnie jest stosunkowo cienka i łatwo może ulec uszkodzeniu, to wytworzona przy użyciu kwasu azotowego jest kilkukrotnie grubsza i bardziej jednolita. Dzięki temu metal uzyskuje świetną powłokę chroniącą go przed korozją i działaniem innych czynników chemicznych mogących degradować jego powierzchnię. Powierzchnia pasywna jest również samo naprawialna tzn. w przypadku jej niewielkiego uszkodzenia np. poprzez zarysowanie po pewnym czasie uszkodzone miejsce pokryje się nową warstwą tlenkową. W przypadku procesu [trawienia] zmienia się struktura powierzchni detalu natomiast pasywacja chemiczna nie powoduje zmian makroskopowych, jej efektem jest jedynie polepszenie odporności.
Pasywacji mogą zostać poddane prawie wszystkie gatunki stali nierdzewnych. Jedynym warunkiem jest to aby zawartość chromu nie była niższa niż 10-11% . W przypadku przedmiotów delikatnych, wysoko precyzyjnych do kąpieli pasywacyjnej dodaje się inhibitorów, które zapobiegają jakiejkolwiek ingerencji kwasu azotowego w strukturę detalu.
Pasywację można prowadzić w takim samym zakresie jak proces trawienia tzn.
- zanurzeniowo
- natryskowo
- przy użyciu żelu pasywacyjnego
Aby proces pasywacji mógł zostać przeprowadzony prawidłowo i skutecznie powierzchnia detalu przed procesem powinien zostać odpowiednio przygotowana tzn. odtłuszczona, pozbawiona resztek materiałów z ewentualnej obróbki ściernej, zaś same spawy powinny zostać zaczyszczone lub wytrawione. Im lepiej zostanie przygotowana powierzchnia tym lepszy efekt końcowy pasywacji. Detal poddany procesowi pasywacji już bezpośrednio po wypłukaniu w wodzie resztek kwasu, ma całkowicie wykształconą powłokę antykorozyjną.
Warstwę pasywną o świetnych właściwościach antykorozyjnych i dużej twardości uzyskuje w się w procesie [polerowania elektrochemicznego].
III. Polerowanie elektrochemiczne stali
Elektrochemiczne polerowanie stali
Elektrochemiczne polerowanie stali można prowadzić w różnych kąpielach, jednakże stosowanie tego procesu na skalę przemysłową wymaga elektrolitu składającego się z mieszaniny kwasu siarkowego i fosforowego. Proces ten zastosowano dopiero po drugiej wojnie światowej dla różnych gatunków stali węglowych i stopowych. Najlepsze wyniki techniczne i ekonomiczne osiągnięto dla stali kwasoodpornych, których polerowanie mechaniczne jest bardzo uciążliwe.
Typowy układ do elektrochemicznego polerowania stali przedstawia rysunek 1.
Proces polerowania elektrochemicznego realizowany jest w wannach lub innych zbiornikach, które wypełnione są odpowiednią kąpielą – mieszaniną kwasów. Przedmiot polerowany (anoda) zanurza się w kąpieli i podłącza do dodatniego bieguna źródła prądu stałego. Wewnątrz wanny znajdują się również katody, które są podłączone do ujemnego bieguna źródła prądu. Katody i anody zanurzone we właściwej kąpieli tworzą zamknięty układ elektryczny. Podczas przepływu prądu przez ten układ, przy zachowaniu odpowiednich parametrów procesu, następuje wygładzenie, wypolerowanie powierzchni elektropolerowanego przedmiotu.
Ilość metalu usuwanego z polerowanego detalu jest proporcjonalna do gęstości przepływającego prądu.
Wygładzanie powierzchni
Rysunek 2 przedstawia wygładzanie powierzchni, jakie następuje podczas procesu polerowania elektrochemicznego. Powierzchnia materiału nie jest płaska. Występują na niej mikrowzniesienia (A) i mikrowgłębienia (B) o ostrych krawędziach. W trakcie procesu elektropolerowania następuje intensywne rozpuszczanie w obrębie mikrowzniesień nazywanych wierzchołkami chropowatości powierzchni. W obszarach mikrowgłębień proces zachodzi znacznie wolniej. Wynikiem tak przebiegającego procesu w różnych obszarach jest znaczne wygładzenie powierzchni materiału oraz zaokrąglenie ostrych krawędzi. W efekcie procesu elektrochemicznego polerowania uzyskuje się największą odporność korozyjną materiału.